Have you ever dreamed of seeing your fashion design come to life, turning your creative ideas into a wearable piece? This exciting journey requires more than just inspiration—it demands meticulous planning and clear communication. Choosing the right supplier and conveying your vision accurately are crucial steps. Ready to transform your concept into reality? Let’s dive into the detailed process of bringing your fashion design from concept to physical sample, ensuring every detail is captured perfectly.
Concept to Information
Develop a Detailed Tech Pack
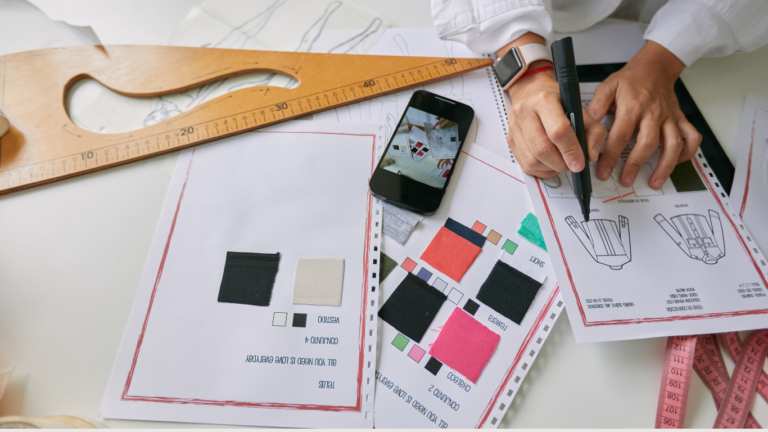
A tech pack is essential for conveying the details of your design. It includes:
- Design sketches with clear and detailed drawings of your design.
- Construction details that inform how the garment should be assembled.
- Materials with detail information of fabrics, trims, and other materials. You can also include the fabric/trims supplier contact details to ensure the sample is made with the exact materials you choose.
- Measurements, such as length, chest, waist, hem, armhole, etc. The more detailed, the better, though you can leave some details to the pattern maker if necessary.
- Placement of brand label and care label.
BTW, while a detailed tech pack is ideal, you can also provide photos, screenshots, or physical samples with specific adjustments. The more detailed the information, the less back-and-forth will be needed, saving time and improving efficiency. As far as I know, the more detailed information with fabric ready, the faster the sampling to be processed.
Source Fabric & Confirm the Fabric to Use for the Sample
Consider what fabric to use for the sample and also take into consideration on the fabric cost. And inform your supplier of the fabric details so they can source it accordingly, or you can source the fabric yourself.
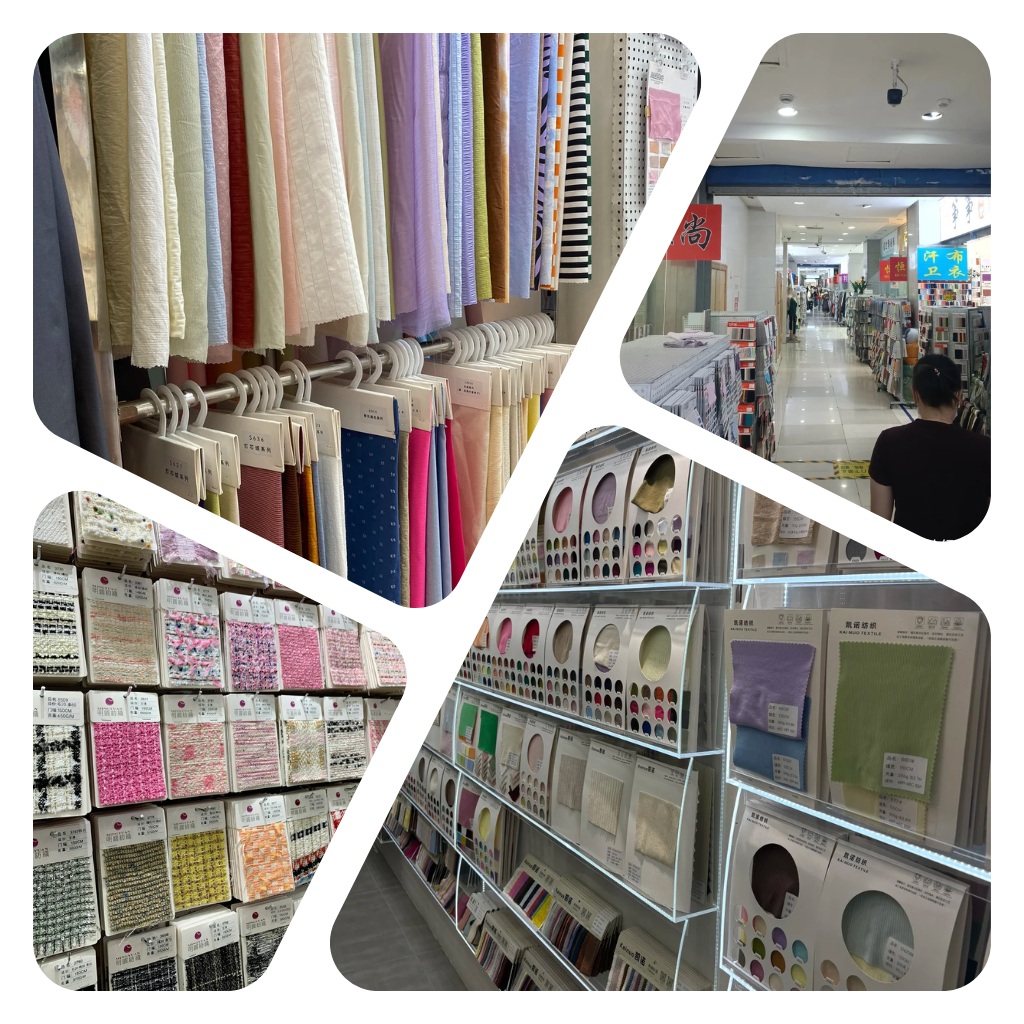
Prepare Print and Embroidery Artwork
If your design includes prints or embroidery, create high-resolution digital files of your designs. Also, consider the size and placement of these elements.
Choosing the Right Partner for Sample Making
Factory
Most suppliers have their own sample rooms. Having the factory make your sample can be cost-effective, and sometimes the sample cost can be refunded if you place a larger order. They can also assist with fabric sourcing. However, factories prefer larger, stable orders. If your orders are small or irregular, they might not prioritize your samples, leading to longer wait times.
Sample Room
If you are just starting out, or if you have your own factory and only need a sample, you might consider a sample room. Sample rooms are dedicated to creating high-quality patterns and samples, but they typically only handle the pattern making and sewing. You will need to provide all the necessary fabrics and materials. Sample rooms usually charge more, and you will need to cover both the fabric and sample costs.
Just Wait for the Sample
Once all the information is gathered and provided to the supplier, the remaining work is in their hands:
Create the Pattern
When you have the tech pack, you can send to your supplier. They can start working on the pattern while waiting for the fabric/material.
Cut and Sew
Once the fabric arrives, it will be cut according to the pattern and specifications, and the seamstress will sew the samples.
And the physical sample is finished and ready to ship to you.
By following these steps, you can efficiently turn your fashion design concept into a tangible sample, ready to impress and inspire. Ready to start your journey? Contact me today to see how I can help you bring your designs to life seamlessly.
How I Can Help
Clothing production is complex, especially if you’re unfamiliar with the industry. Distance and language barriers can make communication and follow-up challenging. Having someone on the ground in China can simplify this process significantly.
I offer the following services:
Fabric Sourcing
I can help you source fabrics at the start of your sample development. When you send your tech pack to the sample room or factory, the fabric will already be decided. This reduces development time, as the factory only needs to purchase the specified fabric and can start making the sample immediately. Since sample rooms don’t handle fabric sourcing, I can purchase and send the fabric directly to them.
Communication & Follow-Up
I can manage communication with the factory and fabric vendors. I can help follow up the entire production processes to make sure everything is on track.
Quality Control & Necessary Errands
I can take measurements and check the quality , handling any other necessary errands to ensure the process runs smoothly.
Customized Services
My services are flexible and can be tailored to meet your specific needs. Let’s explore how I can best assist you.